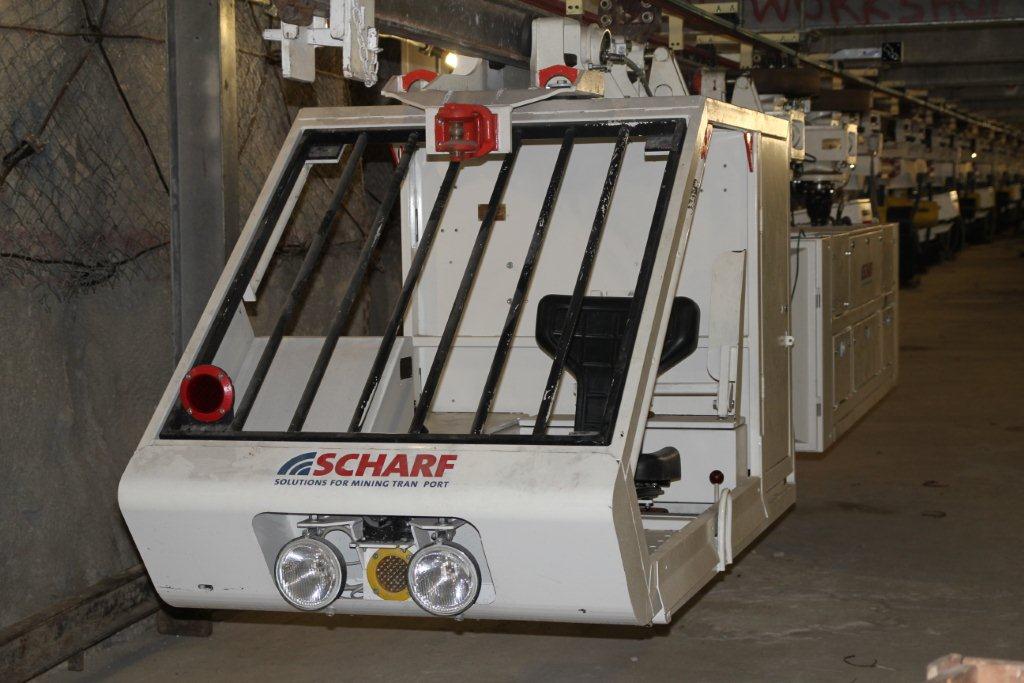
Convincing mines to spend more money up-front on the expectation of lower life-of-mine costs is what one South African supplier is working hard to do.
It’s a dilemma for both seller and purchaser when new technology comes along that looks as though it should be better—and is declared by the seller to be better—but which requires the buyer to dig deeper in his pockets in the short-term. The mining industry is well known for its conservatism and a preference for sticking with what it knows: after all there is a lot to be said for reliability, even if it does come at a price. Fortunately, though, knock on enough doors and someone, somewhere, will be found who is willing to try something new.
This has been the strategy of SMT Scharf Africa while marketing its electric monorail transport system (EMTS). “Globally,” says managing director of SMT Scharf Africa Wayne Busch, “SMT Scharf is most closely associated with coal mining. But in South Africa—and neighbouring countries for that matter—we have found a niche in hard rock mining operations that go underground in search of gold, platinum, chrome and nickel. Here we are finding growing interest in EMTS.”
The role of EMTS is logistical. It isn’t there to remove ore or mining waste but rather to move supplies and consumables underground: bulk materials such as cement, timber or steel for construction, explosives for advancing the mine face. Nor is EMTS likely to be used where a conventional vertical shaft is in place. But where access to the various operational levels is via an incline or decline tunnel (the system can be used where there is a combination of vertical shaft and decline/incline systems),Busch argues that the monorail is literally head and shoulders above the commonly used technology in the decline method of mining.
“There are two main approaches,” he explains. “Either mine cars running on rail tracks are pulled by winches or the mine uses rubber-tyred vehicles, namely UVs and LHDs. Our monorail has countless operational advantages over both; but in a nutshell, winch power finds it difficult to cope with changes in direction—whereas a monorail can negotiate tight curves with ease—and with winch power you also have double handling, which costs time and adds manpower resources. Alternatively, rubber tyres are quickly ineffective when the slope exceeds nine degrees or there is surface water in the tunnel. Our monorail can operate comfortably at 30-degree inclines.”
It has to be accepted that EMTS is almost certainly going to go into green field mines, as it is unlikely that any mine would abandon the millions invested in the current way of doing things, however great the benefits. But in new developments—and in Southern Africa there are plenty—the benefits of an electrical powered monorail can immediately be felt.
“There is something like a five or six year capital expenditure cycle,” says Busch. “We had a bumper year in 2009 when revenue hit R170 million—twice our normal annual sales. We expect something similar in 2014 as we have many new mining projects currently going through the various feasibility stages that have been costed on using our system.”
So how will these projects benefit from EMTS? First and foremost, by using electricity, all the costs associated with diesel are avoided. Not only the continuously rising price of the fuel itself but also all the cooling and ventilation hardware needed underground to cope with the fumes and the engine and exhaust heat generated. Instead, a typical SMT Scharf monorail power plant is comprised of four non-polluting 30kw motors that only draw power on the upward inclines. When the monorail is going downhill, the motors actually put energy back into the grid. Given that it employs zero-emission transport technology continuously to go from a zero to 30 degree incline, all these factors combined mean that EMTS not only saves its mining clients money, but gives them a much greener footprint too.
Ongoing maintenance costs for a monorail are also considerably less. The electric motors and rolling sets need precious little attention—certainly in comparison with diesel power plants that need regular servicing. Safety is also an issue: should diesel spill or leak, secure footing is compromised—not to mention the inherent dangers associated with winch ropes.
The monorail is designed to carry a standard mine car or skip and can transport six of them at once, giving a total carrying capacity of 20 tonnes. SMT Scharf already has over 20 such systems running at mines run by Impala and a couple of other smaller installations. The longest drift shaft at the moment is three kilometres serving 10 levels, but in other parts of the world there are far longer and more complex rail networks.
While EMTS is not intended to move personnel, SMT Scharf has a sister chairlift system. This has found ready acceptance and there are some 140 installations around Southern Africa. Combine these with the SMT Scharf subsidiary Sareco Engineering and you have a situation where together they hold 85 per cent of the market for personnel chairlifts.
Over the years, since the 1950s, the parent company has metamorphosed several times as it has been acquired by ever larger organisations until in 2007, it went solo once more and listed on the German DAX. In the process it has gathered a much wider range of products and technologies than are being offered in South Africa. However, at the Electra Mining Conference in Johannesburg later in the year, a new diesel powered shunting trolley, known as Sharman, will be launched which Busch believes has a role to play in South African conditions.
“There’s a need,” he says, “for a way of moving supplies and materials into the stopes [the area where the ore face is being excavated usually by drilling and blasting]. This is usually done by winch but in such an inherently hazardous place, anything capable of reducing risk should be welcome. We also envisage many other ad-hoc tasks could be done by Sharman which might otherwise take production equipment out of action.”
SMT Scharf is still a relatively modest operation in Southern Africa although significantly larger than when Busch took over in 2007, when it had a staff of just six employees. Today the turnover is regularly around R85 million and as well as 17 full-time employees, there are another 60 part-timers.
Although most of the equipment has to be imported there is still around 15 per cent of the value added in South Africa and Busch is hoping that this will be increased in the future by expending the fabrication facilities it has at its headquarters near Randburg in Gauteng. No doubt this will be on the agenda to coincide with the expected accumulation of orders for start-up mines after years of speculation.
Written by Alan Swaby; research by Marcus Lewis
DOWNLOAD
SMTScharf-EMEA-July12-Bro-s.pdf